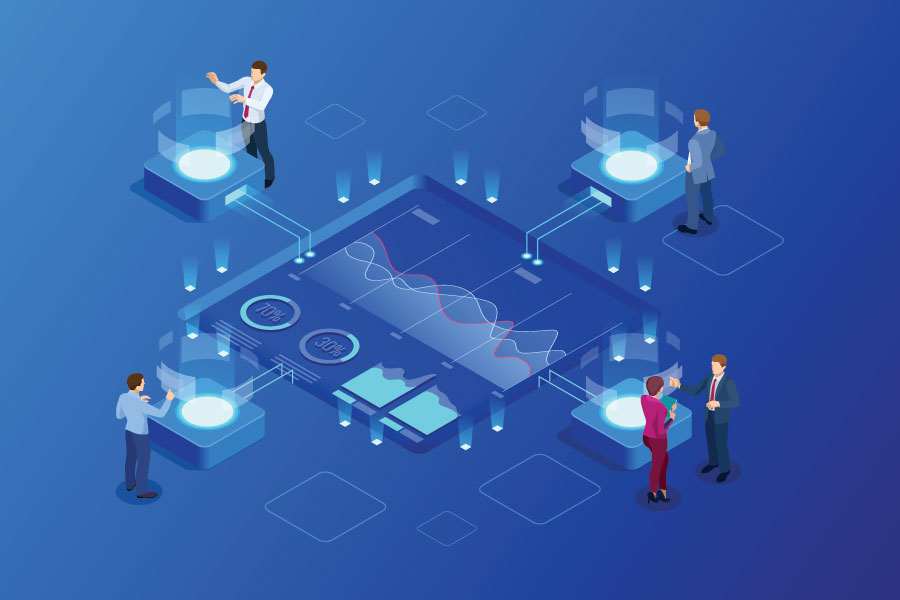
The manufacturing industry relies on its legacy systems and equipment to get work done. This has been the way for decades. A report on the state of the manufacturing industry states that only 26% of manufacturing plants believe implementing new technology is key to optimizing operational performance within their organizations. The report further stated that 7% do not intend to implement any form of technology and are comfortable with their legacy processes but with these processes comes diverse challenges.
These challenges cut across supply chain planning, forecasting, inventory management, and demand management as this post will show.
A Detailed Look at the Challenges Brownfield Facilities Face
It is important to note that the term brownfield refers to plant floors where physical processes are the predominant features compared to digital solutions. These physical processes include the use of paper records, writing boards, operating legacy equipment etc. Within these facilities, the challenges to optimizing manufacturing operations include:
- Lack of accurate historical records – Many initiatives across the plant floor depend on the availability of historical records. From the advanced planning perspective, these initiatives include demand forecasting, inventory management, and supply chain planning. Although paper records may exist dating back a few years, these reams of binders become more difficult to use as the months go by. Thus, with inaccessible or inaccurate data to execute a demand forecasting process to develop future schedules a trial and error approach is relied on.
- Difficulties with analyzing available data – In situations where machine data exists but is curated on paper, aggregating months of paper data to calculate overall equipment effectiveness percentages or effective equipment performance becomes a chore. These difficulties also extend to inventory management when the need to decide available inventory and what is required to meet fluctuating order demands come up. The use of reams of binders provides no analytical versatility which means large and, in most cases, inaccurate estimates are made with every production cycle leading to stockouts and material or ingredient scrapping.
- A supply chain in disarray – Although many brownfield facilities rely on singular suppliers to reduce the difficulties with supply chain management, this isn’t enough to handle the dynamics of today’s market. Today, diverse factors such as increased customer awareness, the need for accountability, and fluctuating demand mean a more diversified supply chain is required. Using old techniques to handle new challenges or manage three or more third-party suppliers is next to impossible. Thus, brownfield facilities end up with low service-levels and no flexibility to meet unexpected demands or complex orders.
- Inadequate Collaboration – Seamless in-house communication within the plant floor is needed to optimize production and ensure everyone is on the same page. The use of conventional or manual planning solutions has led to multiple operators working on the same task. It also provides major bottlenecks for managers who have to come up with plans to optimize operations. Collaboration is also an important feature for managing third-party suppliers and the traditional process of calling ahead of time becomes totally redundant if the supplier is expected to make immediate changes within a limited timeframe.
- Lack of tools for business insight – The first three challenges on the list highlights the difficulties with forecasting which is needed for accurate decision-making. The manual tools used in brownfield facilities deliver limited insight into the future operations of the plant floor. This means in every case, brownfield manufacturers fly blind and simply reinvent the wheel with each production cycle which leaves no room for growth.
Optimizing Advanced Planning in Brownfield Facilities
Although new solutions to digitize manufacturing facilities exist, manufacturers who shy away from using these solutions point at the cost of revamping legacy processes. These reasons are valid because the costs of developing DIY supply chain planning software or platform are astronomical. Besides the initial costs, recurrent maintenance costs and the need for an in-house professional to manage the software are out of reach for the average manufacturer.
This is where subscribing to an agile supply chain planning software comes into the picture.
With cloud-based planning software, you solve the most important challenges your brownfield facilities face with advanced planning. Planning software comes with the tools for demand forecasting, inventory management, and supply chain planning. Software that leverage the cloud ensures that with continuous business growth comes more computing resources to meet your expanding planning requirements. You can learn about selecting the best planning software for your manufacturing facility by downloading this e-book.
We’ve made it easy for you to choose the best capacity planning software for your manufacturing processes.